Our story
Since its inception in 2011, QiOVA has been designing innovating laser processing solutions to help our customers produce in a more effective way.
Our vision has 2 fundamental beliefs :
- Laser is the production tool of the future. Thanks to its unmatched benefits such as high resolution, permanent, contact-less, consumable-less, laser light delivers a superior level of production added value with minimal ecological footprint.
- Throughput is the main driver for broader industry adoption of laser tools. With the large choice of high-power industrial laser available today, the productivity bottleneck lies in the ability to deliver the light to the workpiece in the most efficient manner. Galvanometric scanners reached their speed; better tools are needed for emerging mass applications.
QiOVA’s unique Programmable Multibeam technology makes sure our customers are always processing parts in the most optimized conditions.
VULQ1 modules and systems offer industrials the production tools needed to lead in the 4th industrial revolution.
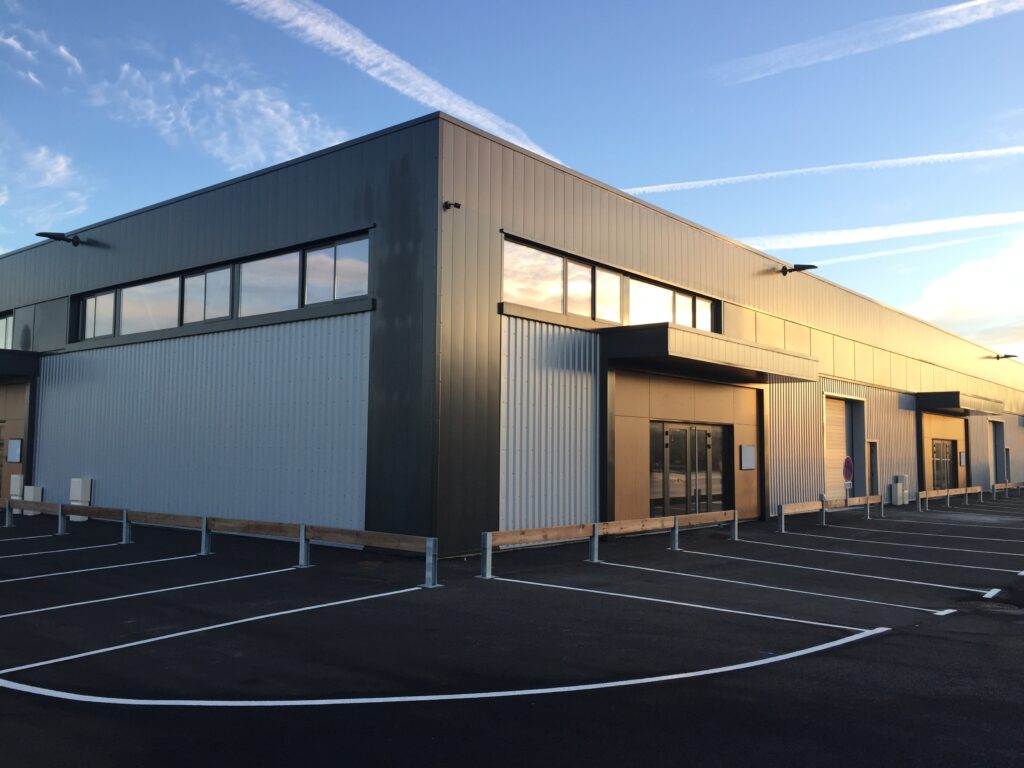
Pionneering multibeam laser technology application to material processing
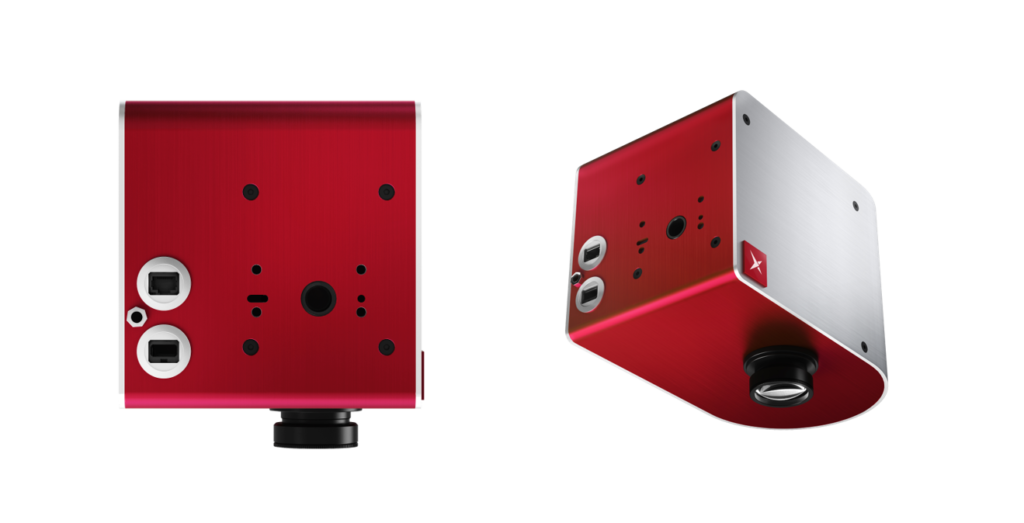
First OEM beam shaping module in the market
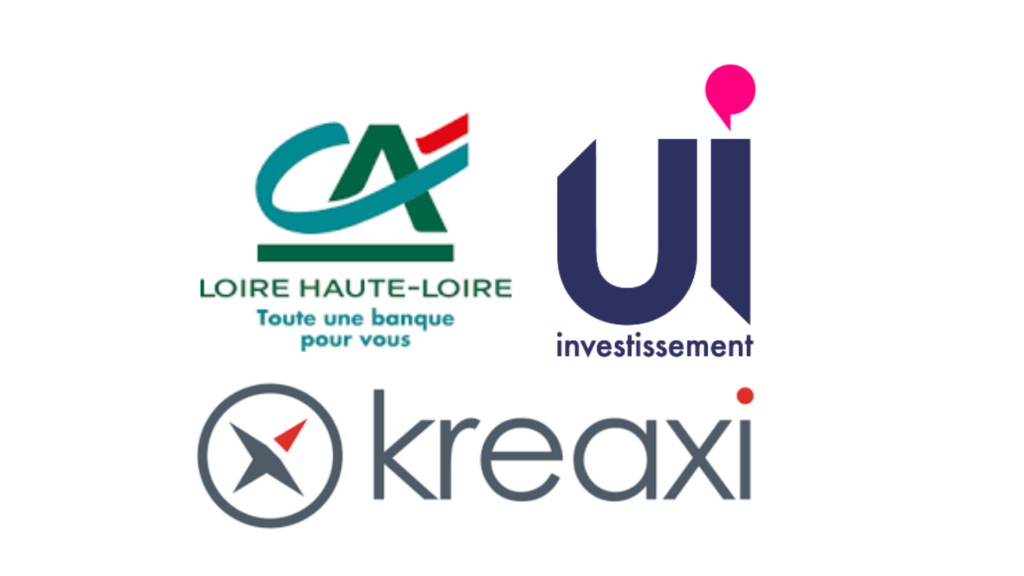
Raised 1,3M€ to boost deployment of multibeam solutions into the market

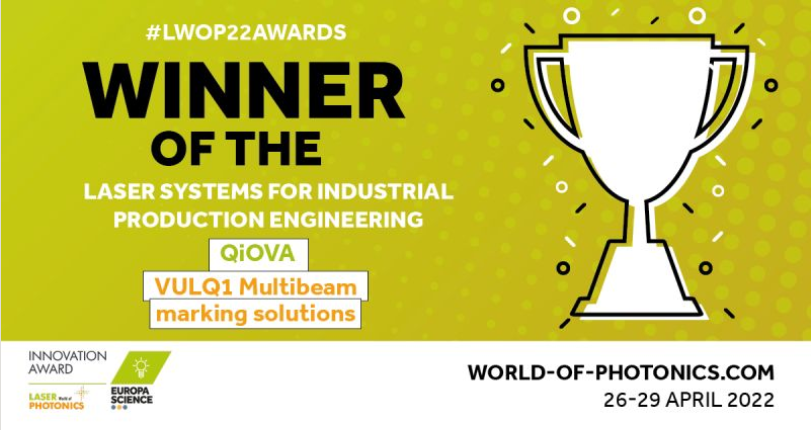
Laser system for industrial production engineering
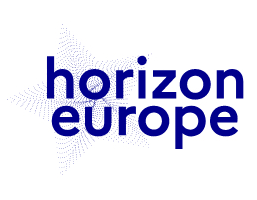
To develop high throughput laser surface texturation
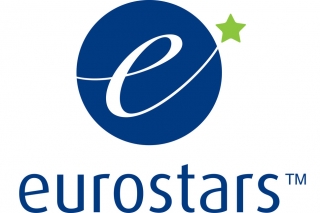
To market novel high security marking system
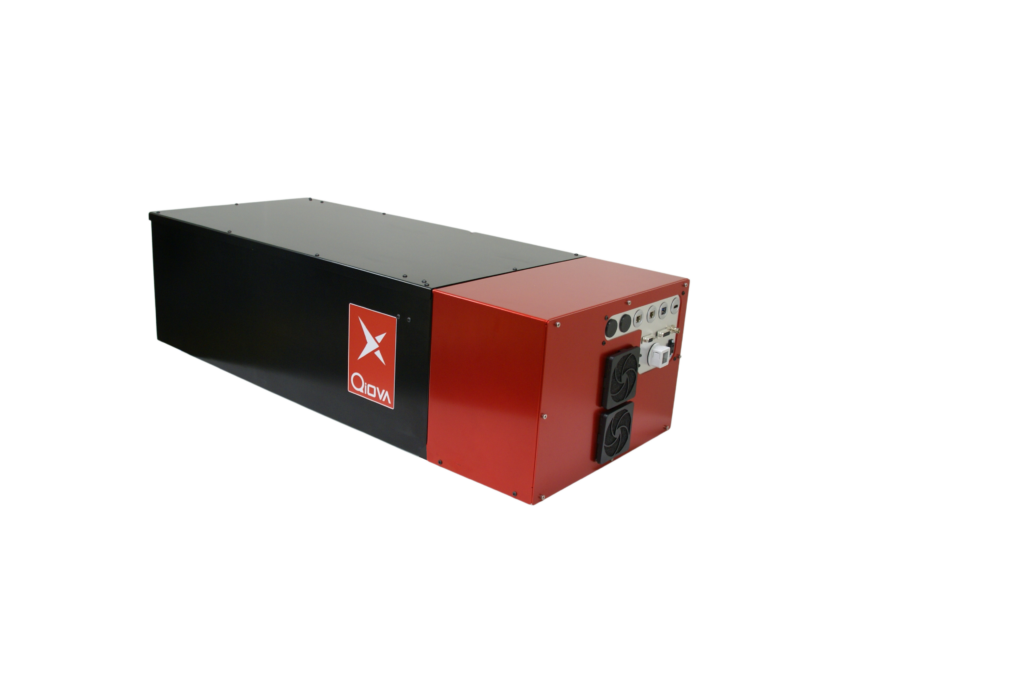
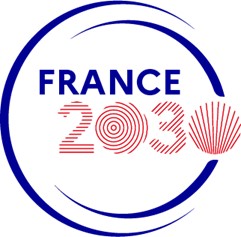
Individual project
Smart laser tools for the industry of the future
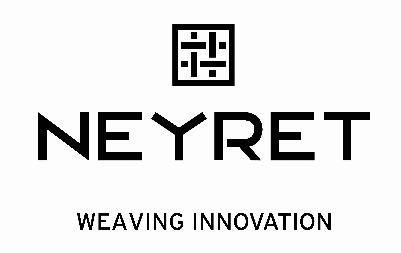
Focus on multibeam solutions for Luxe segment
Industrial group leading round
Our team
CEO
CTO
Head of sales
Software / IT / Quality Manager
Methods technician / After-sales service
Optical Engineer
Test pilot engineer
Administrative
IA PhD student
Operations Manager
Work-study Mechanical Engineering
Work-study IT
Work-study Administrative
Work-study Communication
Our vision
Laser is the production tool of the future
Thanks to its unmatched benefits such as high resolution, permanent, contact-less, consumable-less, laser light delivers a superior level of production added value for materials processing with minimal ecological footprint.
But the way laser solutions are designed today limits their performance.
Once limited by the available laser power, the bottleneck in achieving higher productivity with lasers comes from the sole scanner based beam delivery. Laser processing is like hand writing, a sequential approach where movement speed ultimately defines throughput. Modern galvanometric scanners are approaching the limits set by mechanical inertia.
Multibeam laser processing with VULQ1 unlocks these bottlenecks
Multibeam processing is the combination of dynamic laser beam shaping with VULQ1 and traditional laser beam delivery systems.
VULQ1 programmable multibeam technology allow users to extract unused power and use it on the workpiece to create throughput.
If the process uses 10% of the available power, the potential of process acceleration with VULQ1 is 10x.
VULQ1 programmable multibeam technology also offer new methods to use light, with unique performance
Standard laser processing therefore reaches 3 limits, limiting broader industry adoption :
Economical limit
➡️
There are 2 main contributors :
A long processing time means high production cost.
The process throughput being limited by the laser beam speed, it is increasingly frequent that the laser power used for the process is only a portion of the total laser power, like 10-20%.
As the laser is an expensive part of equipment, the return on investment for the industrial is slower and the initial spending more difficult to justify.
Environmental limit
➡️
Laser processing is much greener intrinsically that most traditional industrial production technique.
But running a laser process that uses 10-20% of its capacity can further lower its impact on environment.
Throughput limit
➡️
The laser process productivity is limited by the speed of the laser beam onto the sample.
The laser beam being small, this translates into a small amount of processed area per minute and long processing time.